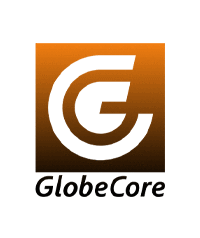
KESIR is the distributor of GlobeCore products in Turkey. Headquartered in Germany, GlobeCore is one of the world leaders in industrial production.
GlobeCore products;
- In the production of bitumen emulsions,
- Transformer oil regeneration, purification
, - In fuel blending, - In the production of biodiesel and
- It is used in the emulsification of almost every material.
The production facility is equipped in accordance with international industry standards: it has robotic plasma metal cutters, automatic welding systems and modern PLC-controlled machines.
What are the advantages of GlobeCore technologies?
First of all, it is an environmentally friendly equipment. It does not emit harmful pollutants into the atmosphere and saves the environment from the disposal or storage of waste oils.
The second advantage is financial. Regular oil treatment prolongs the service life and reliability of oil-filled equipment. It also saves on oil purchase and disposal, maintenance and repair costs, as well as the costs associated with mandatory downtime.
The third advantage is the ease and safety of maintaining and operating oil treatment plants.
For the convenience of the customer, this equipment is mobile (on a trailer, on wheels) or stationary. It is designed to work in special conditions (explosion proof).
The main advantages of oil processing with GlobeCore technologies are:
- Connection to the transformer in accordance with all safety standards (Transformer Safety System);
- Antifoam system;
- Oil sensors;
- Replaceable cartridges (filtration fineness 1, 5 and 25 microns);
- Safe and easily adjustable band heaters with low heat capacity;
- Efficient coagulant-evaporator in the vacuum column;
- Fully automated process Optional remote control and monitoring via smartphone or PC.
Oil Purification
Waste oils are an issue for the global environment. They pollute large areas of land and water bodies, leading to the death of animals and causing serious illness in humans. The most effective solution is oil purification and subsequent re-use of purified oils. Usually oil purification is a multi-stage process consisting of sedimentation, centrifugation, coagulation, selective purification, filtration and combining some of these methods regeneration. Sedimentation cleans oil in special containers using gravitational forces. As a result, it removes solids, as well as free and dissolved water. Centrifugation removes these impurities, and is more effective, since it takes less time. Electrophysical oil purification removes solid contaminants and partly oil sludge and aging products.Sometimes oil purification uses coagulation. But in reality, it only intensifies other approaches by introducing special substances (coagulants) into oil, which promotes the coalescence of impurities. Then the larger particles are easier to remove through filtration, sedimentation or centrifugation. Selective purification is a selective dissolution of undesirable oil components with the help of solvents. After removing impurities from oil the solvents are removed and reused. The main disadvantage of this approach is inability to process oils that contains additives. Since oil additives are absorbed by a solvent together with harmful components, resulting in performance deterioration. Filtration is used in different oil purification equipment.
Oil filtration
Earlier, oil filtration was carried out mainly with the help of filter presses, which removed mechanical impurities, emulsified and dissolved water. Filter press pushes oil through a porous medium that retains water and solid particles. A filter medium is chosen according to the quantity and nature of existing contaminants.
The factors that affect filtration are:
• Viscosity of oil;
• Filter media thickness;
• Filter media surface area;
• Oil pressure.
Now transformer oil filtration is carried out mainly with the help of porous polymer filters. They retain oil impurities and control their particle concentration and particle count, distributing the impurities by size and groups. The diversion from filter-presses was caused by their cellulose structure. Since cellulose particles that entered transformer oil caused a decrease of breakdown voltage and increase of dielectric losses. Polymer porous filters trap more impurities, and lose their absorption ability relatively slower.
Generally oil filtration uses pumps to create pressure to pass oil through a filter partition, which traps solid particles. Magnetic filters work differently. They attract particles of ferromagnetic materials.
Filters provide a required fineness – coarse, medium and fine oil filtration. Also, some filters are replaceable and some have a removable filter element.
Oil filtration does not remove water and dissolved gases. This problem is solved through degassing.
Oil degassing
In service oil should not contain water and dissolved gases. Dissolved gases decrease the overall electrical strength of the insulation system, since gas bubbles often contain electric discharges. Therefore oil degassing is a necessary measure in operation of power transformers and other industrial equipment.
Nowadays degassing of oil by thermal vacuum treatment is the most effective solution. It is realized in two stages. In the first stage in vacuum, there is an intensive release of water vapor and gases. This process removes 60-90% of the initial volume of moisture and gases. The rate of evaporation could be increased by increasing interface between oil and gas phases, and reducing the thickness of the oil layer. Technically, for this process are used Raschig rings, Kerting nozzles, to spray oil into vacuum column.
Oil degassing by ultrasonic cavitation uses a special vibrator under vacuum that forms microbubbles filled with gas and water. The bubbles rise to the oil surface bringing with them gases and moisture.
Producers of power transformers request oil degassing during site installation and during routine maintenance for reliable operation. Transformer oil for good exploitation should not contain gases more than 0.1% by volume.
Oil regeneration
During operation, oil can become contaminated not only with solid particles, water and gases, but also with products of aging and oxidation that significantly reduce its performance characteristics. This contamination is removed through regeneration that improves oil parameters and extends the service life of oil, and the entire transformer by more than 20-25 years.
Often the terms “oil regeneration” and “oil purification” are identified. But in fact they are not the same processes. Oil purification is a part of oil regeneration. But it is also used independently, usually when oil aging has not yet reached a critical level.
Regeneration also removes sludge, acids, asphalt-resinous substances, organometallic and polyaromatic compounds, unsaturated hydrocarbons and decomposition products. The process is stabilized with special additives.
In practical operation, the degree of oil aging is determined by analyzing the acid number. The acid number value determines the following oil characteristics:
• Oils with acid number below 0.25 mg KOH / g;
• Oils with high degree of aging (acid number 0.25-0.5 mg KOH / g);
• Heavily oxidized oils (acid number exceeds 0.5 mg KOH / g).
Oil purification methods listed above cannot remove oxidation and aging products. Therefore, oil is regenerated with the help of adsorbents, which trap acid compounds, asphalt-resinous substances and other products formed during operation. This approach is relatively simple and has a high rate of purification. It can process all currently known types of industrial oils. The adsorbents used for oil regeneration are active carbons, silica gels, zeolites, bleaching clays, etc.
Oil purifiers from GlobeCore
GlobeCore produces CMM oil purifiers. This equipment is designed taking into account all the latest trends and requirements of the market for purification and regeneration of oil products.
They imploy modern technologies of oil recovery:
• Multistage filtration for removal of solid particles;
• Thermal vacuum treatment for removal of water and gases ;
• Adsorbent purification to remove products of oxidation and aging (silica gel, zeolite, Fuller’s earth).
Depending on the oil condition, you can select both oil purifier and oil regeneration plant. One of the best equipment of GlobeCore is rightly considered a CMM-R unit, designed for processing insulating oils directly in a tank of an energized transformer. It regenerates oil through a complex of processes, heating, degassing, vacuum treatment and adsorbent purification, with adsorbent reactivation. The unit uses Fuller’s earth for oil purification .
The oil purifier CMM-P can be connected to an energized and de-energized transformer. The oil is regenerated as it circulates in a closed loop between transformer and oil purifier. The Fullers earth adsorbent removes aging products and sediment that has collected in a tank. This last fact helps to completely remove impurities, which are difficult to get rid of and which then fall into fresh oil and deteriorate its operational properties.
Another important advantage of GlobeCore technology is a repeated reactivation of adsorbent. Fuller’s earth properties can be restored up to 300 times, which is equivalent to 2-3 years of CMM-R operation. In this case, the reactivation proceeds in parallel with oil treatment. Correctly chosen regularity of regeneration prolongs the service life of power transformers, restoring their dielectric strength and chemical composition of electrical insulating oils. Link to access Globe Core products.
click for more detail
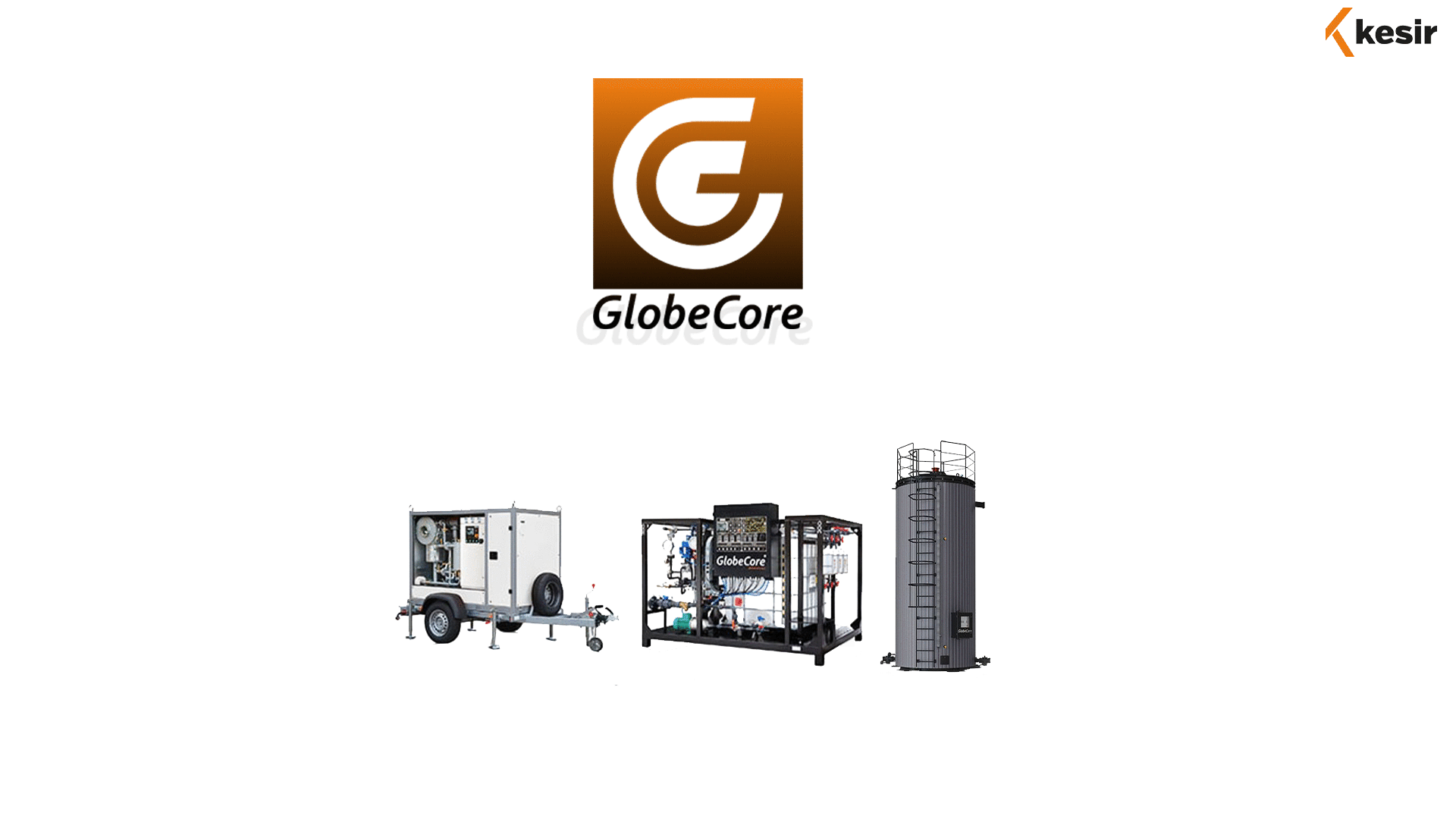